The Drill SFM Calculator helps machinists accurately calculate the speed at which the cutting tool should move relative to the material. Accurate SFM calculations ensure efficient machining, preventing tool wear and workpiece damage, thus saving time and resources.
Formula of Drill SFM Calculator
To understand the output of an SFM calculator, one must first grasp the formula:
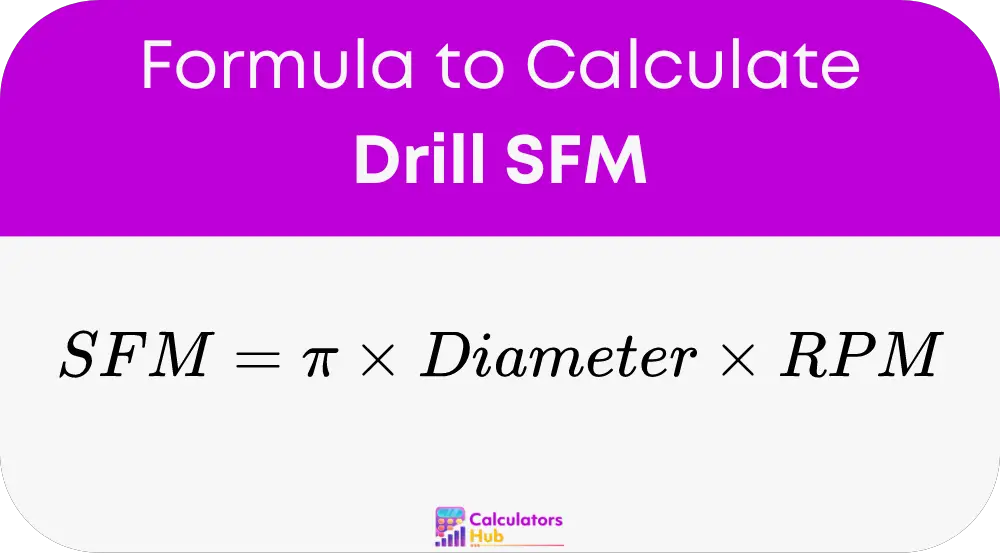
Where:
- SFM is the Surface Feet per Minute, indicating the speed of the cutter’s surface as it cuts the material.
- π (pi) is approximately 3.14159, a critical constant in circular motion calculations.
- Cutter Diameter is the size of the cutter’s cutting end in inches.
- RPM stands for revolutions per minute, the speed at which the cutter spins.
Practical Table of Common Values
To aid quick reference, below is a table featuring common cutter diameters and RPMs with their corresponding SFM values. This table allows machinists to bypass calculations for standard tasks and directly apply these figures to ensure optimal machining settings.
Cutter Diameter (inches) | RPM | SFM |
---|---|---|
0.5 | 1000 | 1571 |
1.0 | 1000 | 3141 |
0.5 | 2000 | 3142 |
1.0 | 2000 | 6283 |
Example of Drill SFM Calculator
Consider a scenario where a machinist needs to determine the SFM for a cutter with a diameter of 0.75 inches spinning at 1500 RPM. Using the formula:
SFM = π × 0.75 ×1500
SFM = 3.14159 × 0.75 × 1500 ≈ 3534
This result helps the machinist set the machine to achieve optimal cutting efficiency.
Most Common FAQs
A1: SFM is critical for determining the best speed to maximize tool life and ensure quality cuts without overheating or material damage.
A2: Incorrect SFM can lead to suboptimal cutting speeds, causing premature tool wear, poor surface finish, or even tool breakage.
A3: Yes, softer materials generally require higher SFM, while harder materials might need lower SFM to avoid tool damage. Always refer to material-specific guidelines.