The Casting Shrinkage Calculator is an essential tool for foundries and manufacturers involved in casting processes. This calculator helps determine the shrinkage percentage that occurs when a casting material transitions from its liquid state to a solid state. During this phase, metals and other materials often decrease in volume, which can affect the final dimensions of the casting. By accurately calculating shrinkage, manufacturers can adjust their molds and production processes to achieve the desired dimensions and minimize waste.
Understanding casting shrinkage is critical in industries such as automotive, aerospace, and metalworking, where precise specifications are essential. The Casting Shrinkage Calculator provides insight into the shrinkage behavior of different materials, allowing for better planning and quality control.
Formula of Casting Shrinkage Calculator
The formula for calculating casting shrinkage percentage is:
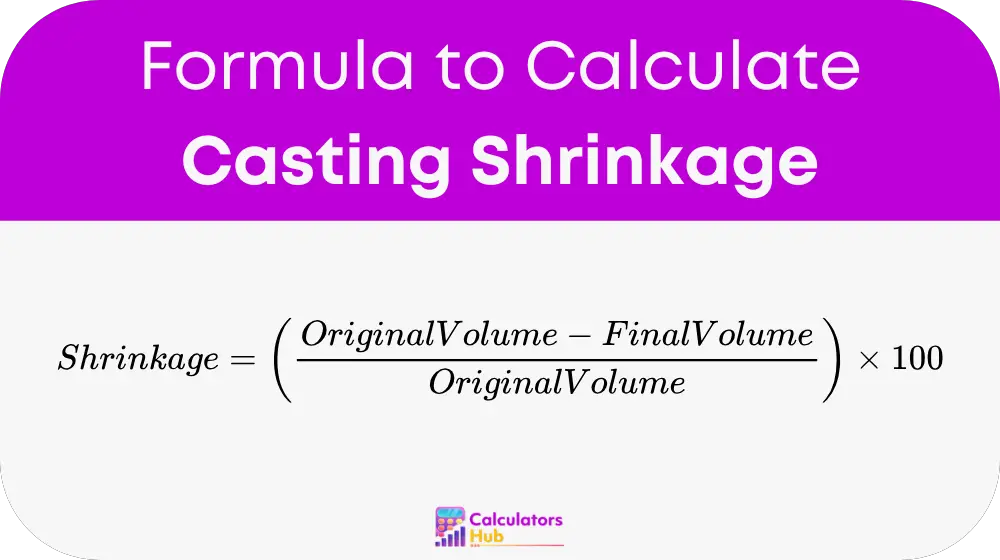
where:
- Casting Shrinkage (%) = Percentage of shrinkage experienced by the casting
- Original Volume = Volume of the casting material before it solidifies (in cubic units, e.g., cubic inches or cubic centimeters)
- Final Volume = Volume of the casting after it has cooled and solidified (in cubic units)
This formula enables users to quantify how much the volume of the material has reduced after solidification, which is crucial for achieving accurate final product dimensions.
General Terms Table
The following table includes general terms related to the Casting Shrinkage Calculator. Familiarity with these terms can help users better understand the context and application of the calculator.
Term | Definition |
---|---|
Casting Shrinkage | The reduction in volume of a casting material as it transitions from liquid to solid state. |
Original Volume | The volume of the casting material prior to solidification. |
Final Volume | The volume of the casting material after it has cooled and solidified. |
Shrinkage Rate | The speed at which the material shrinks during the cooling process. |
Mold Design | The shape and structure of the mold used to form the casting. |
Tolerance | The permissible limit of variation in a physical dimension. |
Example of Casting Shrinkage Calculator
To illustrate how to use the Casting Shrinkage Calculator, consider the following example:
Suppose a manufacturer is working with aluminum. The original volume of the aluminum before solidification is 500 cubic centimeters, and after cooling, the final volume is measured at 480 cubic centimeters.
- Apply the formula: Casting Shrinkage (%) = [(Original Volume – Final Volume) / Original Volume] × 100Casting Shrinkage (%) = [(500 cm³ – 480 cm³) / 500 cm³] × 100Casting Shrinkage (%) = [20 cm³ / 500 cm³] × 100Casting Shrinkage (%) = 0.04 × 100Casting Shrinkage (%) = 4%
In this example, the casting experienced a shrinkage of 4%. This information is crucial for adjusting the mold design to compensate for the expected shrinkage during the casting process.
Most Common FAQs
Calculating casting shrinkage is vital to ensure that final products meet specific dimensional requirements. Understanding shrinkage allows manufacturers to adjust their mold designs, preventing defects and ensuring quality control in the production process.
To minimize casting shrinkage, manufacturers can use techniques such as controlling cooling rates, optimizing mold designs, and selecting materials with lower shrinkage rates. Additionally, using additives or modifying the casting process can also help reduce shrinkage.
No, casting shrinkage varies depending on the material being used. Different metals and alloys have unique thermal properties and shrinkage rates, which is why it is essential to reference material-specific data when calculating shrinkage for various casting processes.